
The Resourceful Sailor Reinstalls a Classic Electronic Autopilot
It’s been a little while since we last heard from The Resourceful Sailor, but he’s back from his most recent sailing adventures, and we’re curious to find out what his latest boat jobs have entailed.
When I bought Sampaguita, a 1985 Pacific Seacraft Flicka 20 sailboat, in 2013, she came with a Navico Tillerpilot 1600 electronic autopilot. The previous owner claimed it did not work. It was wired directly to the battery without a fuse, and would strain the SeaVolt starting battery, which was also the house battery. Initially, I unhooked the wires from the battery for safety, coiled them up, and stowed them in the cockpit locker. The Navico, I put in dry storage.
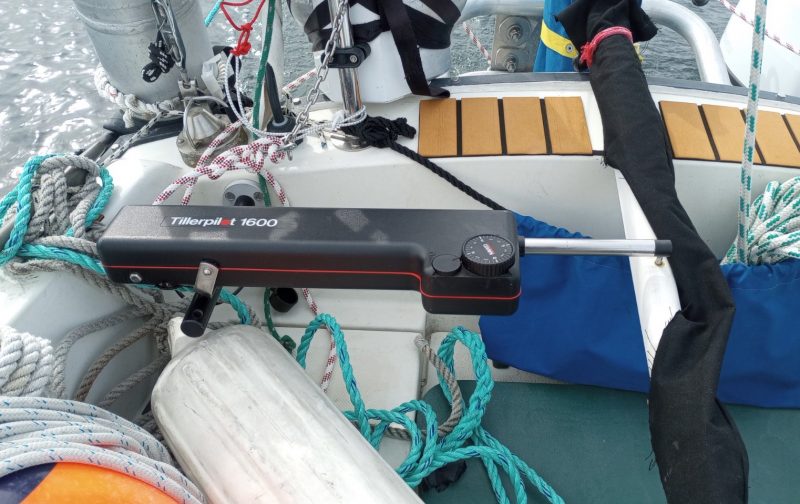
It took me 10 years to see for myself if it worked. As my sailing programs and electrical system evolved, energy was less of an issue. As my storage space also changed, the Tillerpilot needed to be useful or be gone. Other boats I’d recently sailed on, Breskell and Inook in particular, had autopilots, and I was enlightened regarding their convenience. Buying a new unit for Sampaguita was unlikely, but if the one I owned already could be rejuvenated; that seemed sensible.
A previous owner had installed a cantilever bracket and power socket specific to the Tillerpilot 1600 on the side of the cockpit. I had left it in place all these years, and it was a sound and still relevant installation. I needed to safely rewire the connection to the battery, figure out if the claim of inoperability was correct, and install a new tiller pin.
First things first: I needed juice to test the unit. I reconnected the plug to the battery. With the updated electrical system, there was a fused power post. I kept it simple for testing purposes and would create a more permanent connection if the unit was operational. I plugged in the Navico and turned it on. At first, the actuator arm moved out and then retracted. Then it seemed to freeze and stay in the retracted-all-the-way-in position. However, I could hear a ticking sound from the unit as if it were trying to operate.
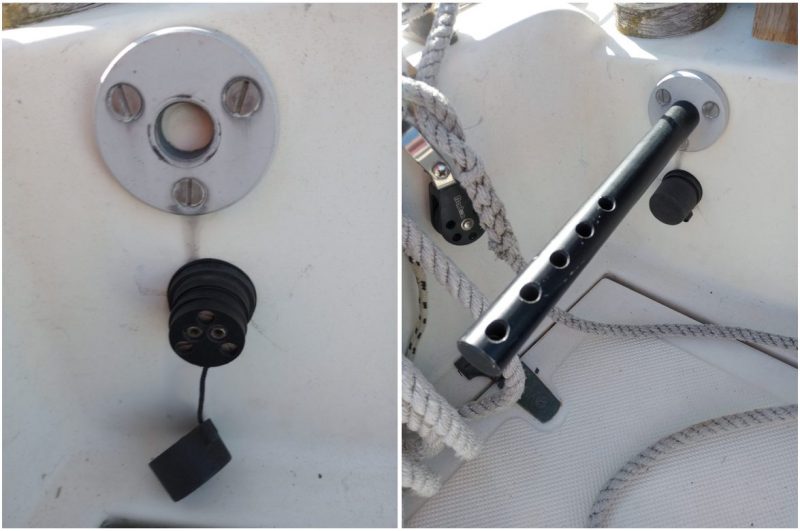
Since I had nothing to lose, I decided to look inside. Obsolete electronics from the 1980s hold no warranty. It was easy to open with nine straight-blade screws, and I was amazed at how simple and immaculate the innards were: still well-greased and clean. I attempted to understand how the unit worked and what might be causing it to bind in the retracted position.
I carefully inspected the arm, the gears, and the guide bars. They looked fine, with no bends or broken or distorted teeth. There appeared to be no visible reason for it to stick. So I muscled it. The moment it unstuck from the all-in position, the motor took over, and the arm began to operate again. Eventually, in its search to align its compass, the arm retracted, and it stuck again. Repeat muscling. Again it became operational.
Uncertain why it was doing this, I called it good. The answer might be not letting the arm retract to the stop. While it wasn’t a foolproof resolution, if I was the only fool using it, I knew the inside scoop. The fix, while a bit tedious, was known and could be repeated if the arm retracted and stuck. (Unless readers teach me better!)
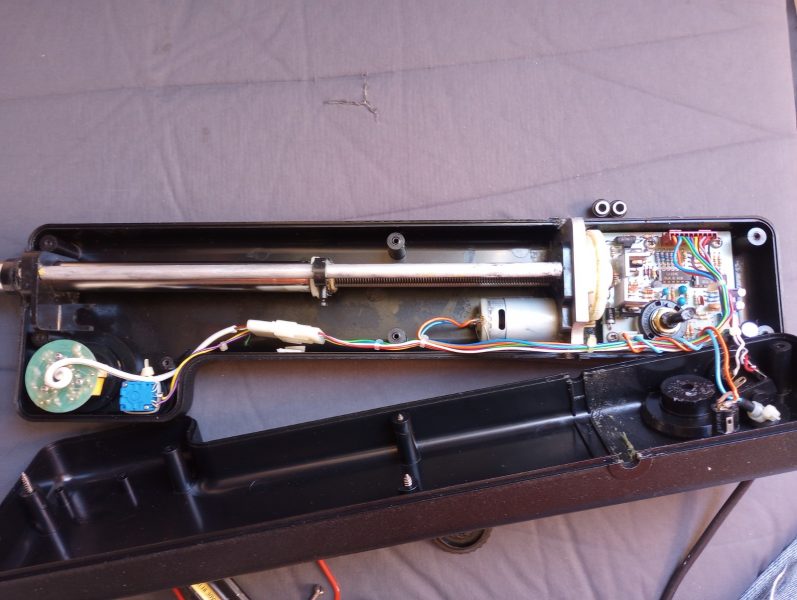
Now that there was, at least for the moment, a functional autopilot, the wires were tidied and secured. The instrument plug was in the cockpit locker, where one of two separate house batteries was, so I decided to simplify things and maintain the connection at the fused power post rather than run it to the cabin circuit panel, which was at capacity. I could reassess this if the value-to-production ratio for an electronic autopilot changed in the future. A safe installation was the primary concern.
A search for compatible tiller pins on the internet turned up exactly what I needed. However, I did not accept what they were offering. You could buy a package of five for $20 plus shipping and tax. Why would I need five? Previously I had found a copy of the Tillerpilot 1600 and 2500 manual on the internet. (It is refreshingly retro, made on an old-school typewriter, typos and all, with simple but comprehensive drawings. I digress.) In its explanation of the installation of the tiller pin and its orientation to the unit, it mentions drilling a ¼-inch hole and epoxying it in. So I found an old ¼-inch stainless steel bolt in my stores. I cut, filed, sanded, and buffed it, using the old tiller pin, still in the now spare tiller, as a model.
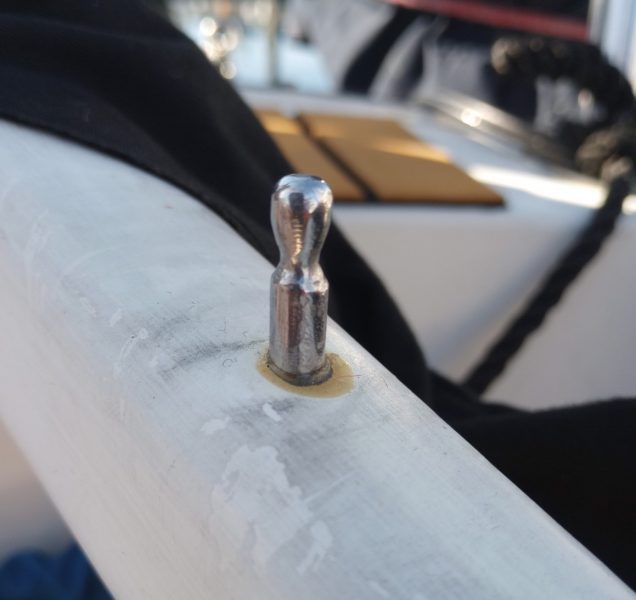
On a 31-day Vancouver Island circumnavigation, I used the electronic autopilot twice. I would have used it at least another time previously, but locating the cantilever post thwarted me. It turned out to be in the bin where I thought it was, but finding it underway proved too troublesome. Of the two times, the first was on Queen Charlotte Strait, from Rough Bay, Malcolm Island, to Port Hardy, Vancouver Island. What started as an incredible day of sailing turned into a flat calm. An introductory experience with the Tillerpilot — it performed very well, and I enjoyed the experience. The second time came when approaching Hot Springs Cove on the west coast of Vancouver Island, fresh from three days and two nights offshore. The wind had died, but the swells rolling in from the ocean and the leftover chop remained. The 1600 did the work, but with much effort, noise, and meandering. The boat, left to itself under power, will always align with the direction of the swells, so the unit was in a constant battle. With a race against light, I took over and sent the Navico to bed.
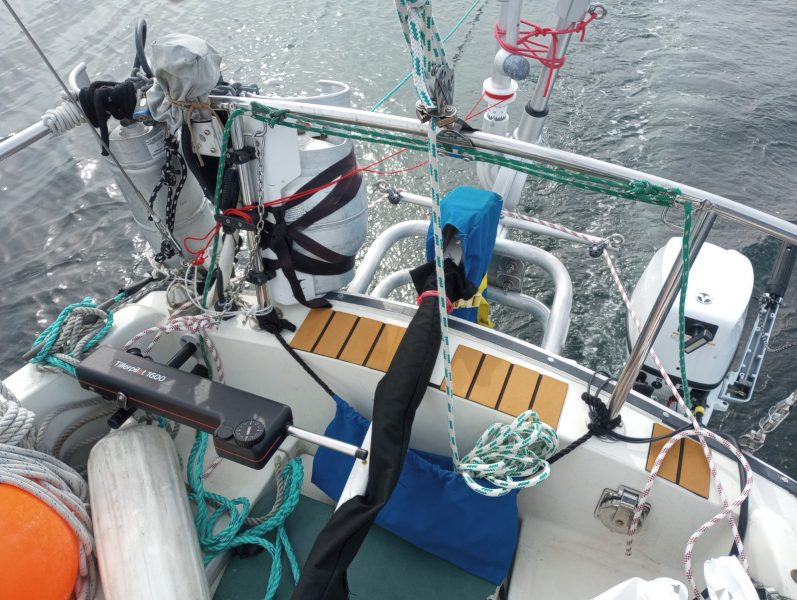
The Resourceful Sailor still has to learn a bit about how to adjust the settings of the Navico Tillerpilot 1600 and when to use it, and remember that it is now an option after all these years. But this is really about reviving a pre-internet but functional artifact. It’s about keeping value, production, and investment in perspective. The best electronic autopilot might be the one you own already. Remember, keep your solutions safe and prudent, and have a blast.
This article reminds me of my first experience with a tiller pilot. It was in May of 1980 on a delivery of Challenger a 34 foot almost new aluminum boat designed for single handing. The owner was Mike Harding (a relative of president Harding from Marion Ohio) who was going to enter the boat in the first single handed Trans Pac race from San Francisco. The boat was equipped with an Aries windvane and the tiller pilot (probably the Navico but I’m not sure). the boat was was heavy helmed and not too much fun to steer and I was short handed with only crew, an inexperienced young woman that was begging for a ride to California on the end of the pier in Hanolai Bay on Kauai the day before my scheduled departure. I was going to single hand the passage but was very relived to have company for the trip. the Aries did a pretty good job of up through the trades which were pretty much 20 to 25 for 8 days or so. This was May and the high hadn’t established itself to much a degree and was farther North than later in the Summer compared to my other trips back to the mainland. We made pretty good Easting but the weather was very cool and cloudy. When we reached the high and began motoring I notice the tiller pilot working pretty hard keeping us on course. While on passages such as this I am obsessed with making things more comfortable or easier to operate. I got the idea of driving the Aries with the tiller pilot through an elaborate rigging of blocks & ropes and a second mini tiller lead to the Aries horizontal vane. This worked very well. The Navico didn’t have to work hard at all and we kept on a very nice compass course with very low power consumption. High pressure system was quite small and we traversed it in 3 or 4 days and went back to the Aries and the vane input until we closed the coast and started to experience stronger winds and seas on our aft quarter. I went back to the Navico for the input to the Aries and was very pleased to have the boat following a compass course and stop the wallowing and over compensating corrections the Aries had to do with the vane’s directional input. I was probably not the first to do this innovation but I was the first I knew about. Subsequently, I have built ‘wind vanes’ of my own design for two vessels I have owned. I am really into the pendulum servo servo steering devices. I built the first of my design for a Dreadnought 32 my wife and I cruised for 4 years cruising a loop from Washington to Equator to French Polynesia to Hawaii and back to Washington from 2006 to 2010. We rarely steered only in & out of anchorages. Most of the steering was done by utilizing a Raymarine tiller pilot inputting the servo part of the wind vane. I like to differentiate between the vane part and the servo part. The servo part is the work horse of the device. The pendulum servo blade and the construct that it acts on does some what subtle while pulling on the lines leading to the tiller. A course error input from a device be it from the ‘wind vane’ or a tiller pilot or the mini tiller rotates the servo blade causing a lifting force that exerts pressure on the carriage that allows the servo blade to swing port to starboard pulling the tiller lines from an attachment point usually equivocal to 20% of the servo blade length. On my Dreadnought the servo blade was 6 feet to the rotation point and (I used a 12 inch quadrant) the resulting force that could be generated at the tiller going 5 knots could be 200 pounds. An important factor if one were to build one themselves is to be aware that the input rotation have a negative feed back. In other words when an off course input causes the servo blade to swing that movement must tend to cancel the input when it moves. If this is not accounted for the servo blade will just continue in it’s swing until it can’t swing anymore and over steering the rudder. I believe I’ve said enough and probably too much even though I could go on about the smaller version I built for my 19 foot boat Bluebird.
Tom,
Thanks for reading! And I’m glad to take you on a trip down memory lane. I have heard of people doing such a thing and have interest in figuring a similar set-up. That being said, I haven’t yet given it enough thought and certainly don’t have a vision of how to do it yet.
Thanks for the inspiration and adding to the research, and shall we say, ‘putting a bug in my ear.”
That is a Windpilot I have and it is new just this spring. So, like most Resourceful Sailor projects, it is a ‘living project.’
Thanks again.